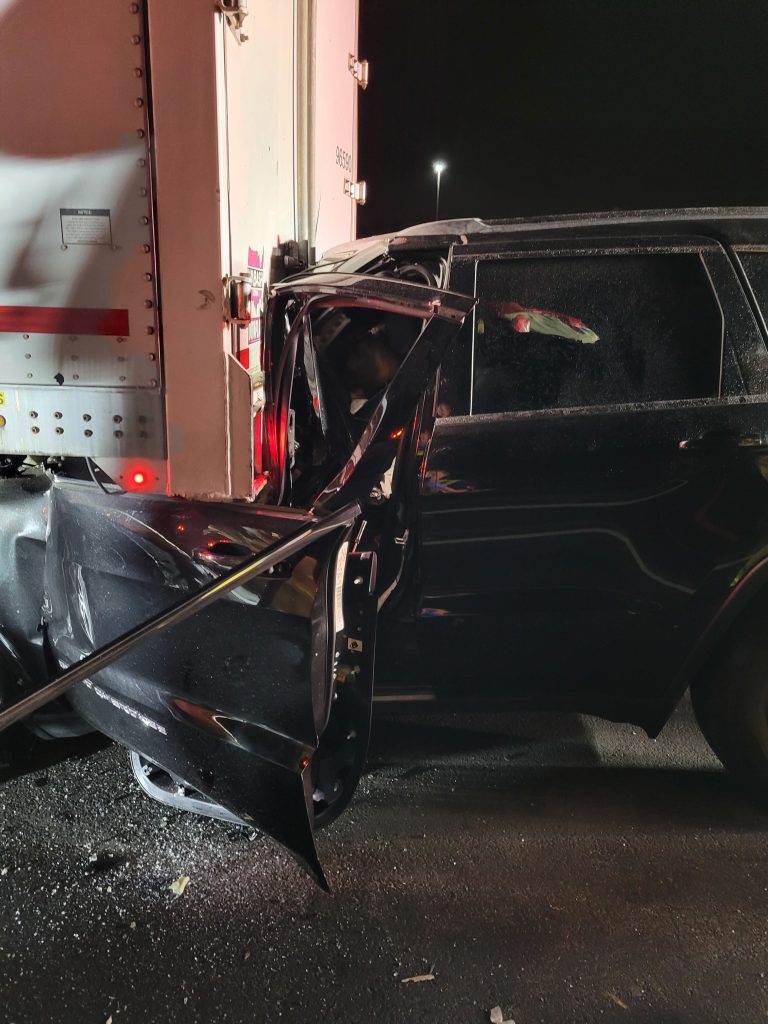
By Jim Spengler, MTI Contributor
Significance
Heavy vehicle under-rides are not rarities. Response to these incidents by extrication capable units should be well ingrained to crew’s muscle memories. But, in this case, the amount of intrusion and entanglement between the vehicles lead to an extended extrication with deviation from the standard response. Also, simultaneous equipment failure and identification of an impalement in one patient complicated tactics. The lessons learned during this call have proved formative in my technical rescue career progression.
Background
A SUV in our response area collided at highway speed into the back of a stationary tractor-trailer. The impact resulted in an under-ride with two SUV occupants, driver and front passenger, trapped and pinned. The back end of the trailer sat midway to the b-post of the SUV. The first arriving engine officer took a photo of the accident and sent it to the incoming heavy rescue officer to expedite tactics and decision making. This was an abnormal action, but justified due to a prolonged response time by the extrication capable unit. The heavy rescue officer, who would lead the extrication, devised a plan and had a complete sense of the scene several minutes prior to arrival.
SOP for Heavy Vehicle Under-rides
Extrications involving heavy vehicles (e.g. buses, cement mixers, tractor-trailers) involve following a stepwise procedure, not unlike passenger vehicle calls. However, gross vehicle weights of up to 80,000 pounds and different vehicle anatomy, leaves less room for error. Briefly, a typical response to a car under a tractor-trailer follows five steps:
- Secure both vehicles and initial patient assessment
Turn off engines and chock trailer tires. Full patient assessment.
- Determine the weight/contents of the heavy vehicle
Knowing the weight of the heavy vehicle is paramount. Rigging and stabilization systems could be utilized to their upper working load limits. Knowing the contents aids in contingency planning for hazardous materials, etc.
- Stabilize the heavy vehicle
The crush of gravity from the heavy object on the smaller car will not stop until acted upon from underneath. Tie-back or stabilize any lean to the heavy vehicle.
- Lower the smaller vehicle, lift the heavy vehicle
Gain distance from the trailer by taking the suspension out of the car, front and rear. Gain more distance by lifting the trailer.
- Separate the smaller vehicle from trailer
Winch the car away from the trailer to create more working area. Now the call becomes a standard passenger vehicle extrication.
Actions and Deviations from SOP
This call in particular, utilized multiple contingency plans. Within the paradigm of the five step process, our crew’s actions were:
- Secure both vehicles and initial patient assessment
Parts of this step were skipped due to error and circumstance. The tractor-trailer’s wheels were never chocked and the engine never secured. Having the initial photo eliminated this procedure entirely from everyone’s brain. Also, the amount of intrusion and debris made it impossible to obtain a full patient assessment. Large portions of both driver and passenger’s bodies were hidden from view. A crewmember entered the back seat of the vehicle to talk and provide care to the patients.
- Determine the weight/contents of the heavy vehicle
The driver stated that the trailer was fully loaded with paper products. 80,000 pounds was the estimated total vehicle weight. The heavy rescue officer called for a sliding rotator to assist.
- Stabilize the heavy vehicle
”Plan A” was to stabilize and lift the trailer with a pair of powered hydraulic lift cylinders. However, as the cylinders made contact with the trailer’s frame, the hydraulic pump experienced a mechanical failure. The failure prevented adequate pressure to build behind the cylinder to lift the trailer.“Plan B” was a more time intensive rigging solution, involving chain, struts, and tie-backs. The end result was a pair of lifting struts and a pair of load capture struts. Once the lift started on step four, the capture struts connected to low psi air, would “chase” the lift struts. Tie-backs were griphoists rigged to the trailer’s rear axles.
- Lower the smaller vehicle, lift the heavy vehicle
The front and rear suspension were fully compressed because of the significant intrusion under the trailer. The only way to gain distance would be to lift the trailer. However, prior to attempting this lift, the crewmember in the vehicle discovered the driver’s leg impaled on bolts from the trailer’s Mansfield Bar. Any movement to lift the trailer, a key part of the SOP, would cause the patient more harm.
- Separate the smaller vehicle from trailer
The only option was to cut the vehicle in place. Not being able to lift or separate the vehicles limited space and slowed extrication significantly. Only one tool at a time could be operated on either side. Crewmembers exhausted the normal complement of cutters, spreaders, and rams. The most complicated problem was the driver. The inherent durability of the Mansfield Bar and its entanglement with various bits of metal, prevented easily cutting it out of the way without further harming the patient. Also, the bolts securing the bar bent during the crash, preventing their removal with an impact wrench. The best option was to move the patient laterally off the impalement. Once crews made enough space to accomplish this, two heavy wreckers slung and lifted the trailer. With the trailer suspended and the impalement mitigated, crews could finish extrication and remove both patients.
Takeaways
- Disciplined approach
The picture of the scene sent prior to arrival caused me and others to skip steps. For example, the tractor engine was running the entire call. This presented a mitigatable hazard to those on scene. My first step should have been to secure the tractor and chalk its wheels. It is an elementary first step that I skipped because my brain was primed with the scene size-up while still en-route. This was a humbling error.
- Task fixation
The mechanical failure was unexpected. I did not expand my focus to fully troubleshoot the problem. There were components to the hydraulic system not in my immediate view that went ignored. Once officers called for a new plan, it was too late to attempt a fix. Later investigation was unable to replicate the failure, but I regret not troubleshooting completely all the same.
- Calm demeanor
Composure and chaos are infectious. The initial failure was a pivotal moment that changed the pace and feel of the call. All felt an increased sense of urgency due to the unsuccessful first lift. Ten minutes to free critical patients became twenty with the new stabilization plan. Twenty minutes could become forty with a panicked response. All crews reacted methodically and professionally to the benefit of the patients.
- Time management
During the extrication, I lost track of time. However, I observed my officer keeping an exacting account of time, minute by minute. It was an important lesson in preventing sunk cost fallacy. If he observed a tactic not working, he called for the next tactic backed by objectivity. It was something I could have done at times, instead of spending too long with an ineffectual technique.
- Mental endurance
Zero “advanced” techniques contributed to successful extrication. The only solution was cutting, prying and pushing metal components piece by piece. This was simple, not easy. It was mentally taxing to observe such slow progress. Surrendering tools in a rotation was necessary to prevent mental fatigue and to check the ego.
- Be an expert
Every tool imaginable came off the rig during this call. The public expects subject matter experts. Not knowing how to use a tool, execute a technique or what tools are available would have been a liability. Being proficient in multiple contingency plans aided a positive outcome. Once plan A fails, immediately knowing what plan B, C, etc are is immensely valuable. Not honing skills and pushing continuous improvement every shift is inexcusable.
- Get resources early
The rotator on-scene was the linchpin of the operation. It freed personnel and was the quickest, safest lifting/stabilization option. Those in charge had the experience and humility to make an anticipatory request. Better to have the rotator and not need it, than the other way around.
- The role of fate
If all went to plan by initially lifting the trailer, the driver would have bled to death. One bolt was millimeters away from the femoral artery. I’m not sure if it is fate, luck or divine intervention that both patients survived. But, things will happen beyond your control, for better or worse.
Jim is a career firefighter for a department in the DC metropolitan area. Jim completed a M.S. in Exercise Science in 2013.
Want to be a paid, MTI Contributor? Email a current resume and three specific topic ideas to rob@mtntactical.com. Writing topics can include fitness, nutrition, quiet professionalism, leadership, and all areas of safety and professionalism in the mountain and tactical worlds.